Ishida Delivers Total Solution for Crisp Packing
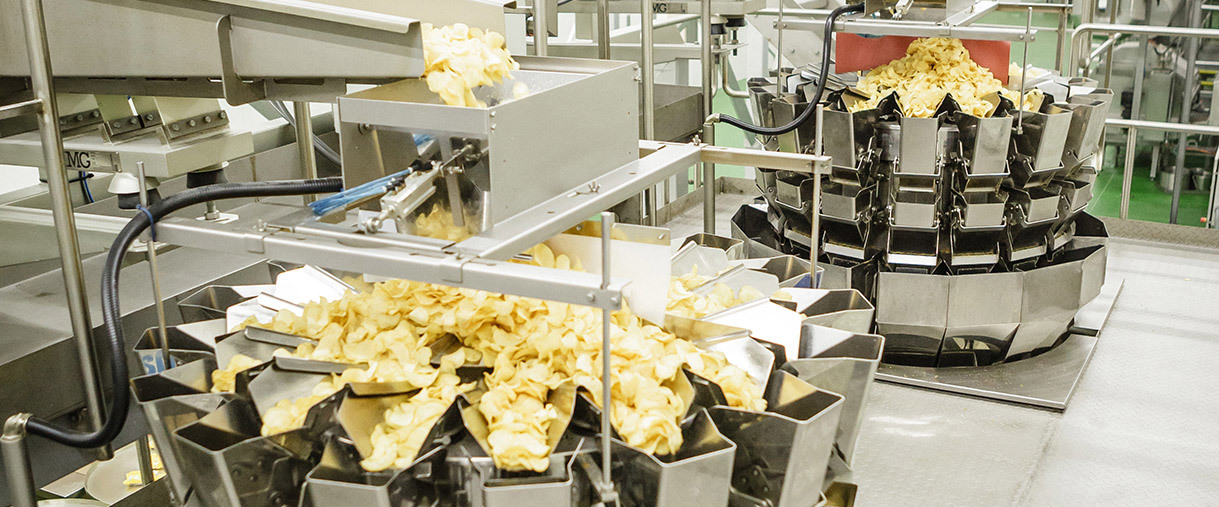
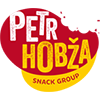
Ishida’s global leadership in snack packing solutions is ideally demonstrated by the complete potato crisp packing line installed at leading Czech manufacturer Petr Hobža at its factory in Strážnice in the Czech Republic. The Strážnice factory produces around 600kg of crisps every hour, the equivalent of 10,000 60g bags.
Facts and Figures
Efficient
Delivering pinpoint accuracy to within 0.1g of the target weight.
Flexible
The 16 head multihead weigher is operating in twin mode, with eight weigh and booster hoppers feeding each of the two Astro bagmakers. Handling two bag sizes of 60g and 175g, the line is achieving speeds of 180 and 110 packs per minute respectively.
Accurate
Overall efficiency levels are close to 100%.
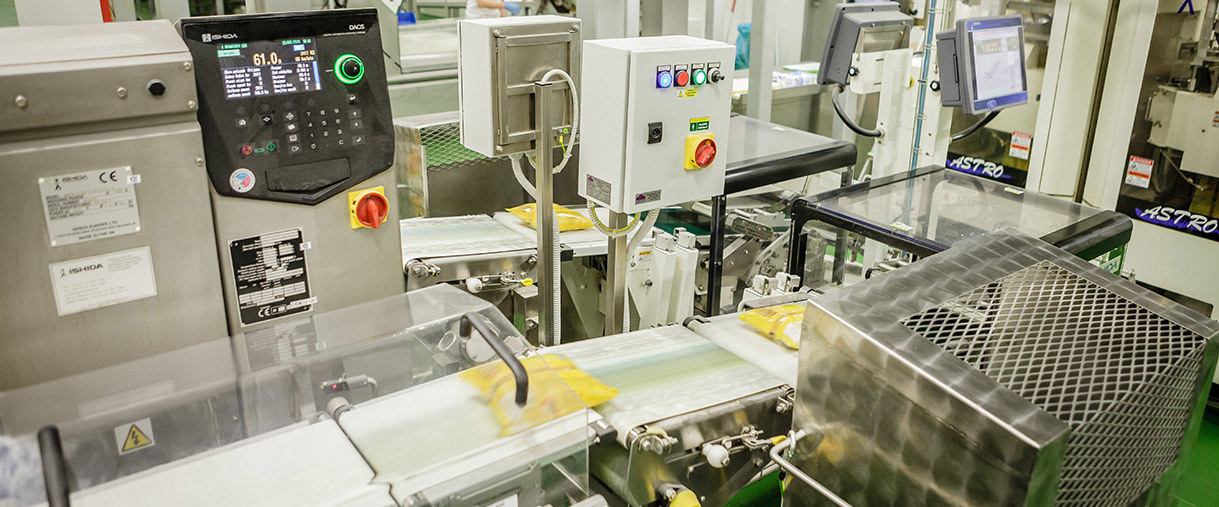
Challenge
Czech manufacturer Petr Hobža came to Ishida to supply a complete integrated potato crisp packing line. The customer requirements for accurately weighed and seal checked bags plus fast payback, reliability and local support made Ishida the first choice supplier.
Solution
The fully integrated line comprises a 16-head Ishida CCW-RS-216B multihead weigher, and two Astro bagmakers, TSC-RS seal testers and DACS-G checkweighers incorporating Ishida’s unique IDCS data capture and production monitoring software.
The 16 head multihead weigher is operating in twin mode, with eight weigh and booster hoppers feeding each of the two Astro bagmakers. Handling two bag sizes of 60g and 175g, the line is achieving speeds of 180 and 110 packs per minute respectively, delivering pinpoint accuracy to within 0.1g of the target weight, with overall efficiency levels close to 100%.
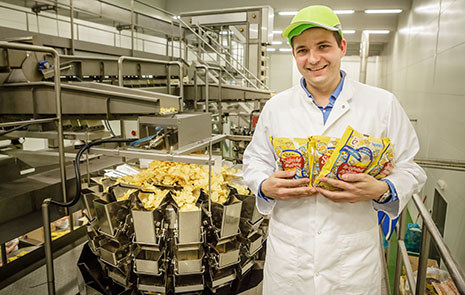
Ishida’s reputation for world-class snacks packing solutions is well established. The accuracy of the equipment alone fully justifies this. Practically zero giveaway is an essential requirement in an operation such as ours, where we are producing some 25 million packs every year.
While ensuring effective quality control monitoring for the integrity of each sealed bag, the Ishida seal tester also provides valuable feedback for the overall production of the potato crisps. A sudden difference in the amount of seal rejects may indicate that the tube size of the batch of potatoes has changed producing larger potato chips that can directly impact on the performance of a packaging system, and action can be taken immediately to adjust production accordingly.
This high level of monitoring is further supported by the Ishida Data Capture System (IDCS) which records and analyses data from every pack that goes across each checkweigher to provide fully customisable real-time production information and displays the line’s Overall Equipment Efficiency (OEE) in terms of availability, performance and quality.
The installed Ishida multihead weigher and bagmaker combination has been specifically designed for snacks applications. As well as the proven high accuracy of Ishida’s multihead weighing technology, the Astro bagmaker features servo-motors and software controlled variable seal time, jaw temperature and pressure for the effective sealing of each pack.
In particular, stripping plates clear the seal area before sealing which ensures the highest pack quality, while servo driven and vacuum assisted pull down belts enable accurate and consistent bag lengths to optimise film use and pack presentation.
As part of automating our processes, it is essential that we can ensure that every bag is accurately weighed and correctly sealed.
Ishida Snacks Packaging Solutions
Ishida Snacks Packaging Solutions
A user-friendly colour touch screen allows easy operation, self-diagnostics and simple and rapid transfers between bag types and film, all of which help to minimise the system’s downtime.
The reliability of the equipment is another important factor for a line that is in operation 16 hours a day, five days a week, while the local support provided by Ishida is a further significant advantage.
'That is why we select equipment such as Ishida’s which will deliver the best performance and the fastest return on investment and which will ensure we continue to achieve the high standards that have characterised our success to date. Having a single supplier for the entire line can respond quickly means that in the event of a problem, the issue can be speedily sorted so that the line is up and running again,' explains Petr.
Download case study


Speak to an Ishida expert
Every business has its own challenges; ours is to help you overcome yours. Working smarter, faster, together, we can help you achieve higher standards and get your products retail ready quicker.