Ishida Inspection Systems Ensure Immaculate Packaging for Crisps
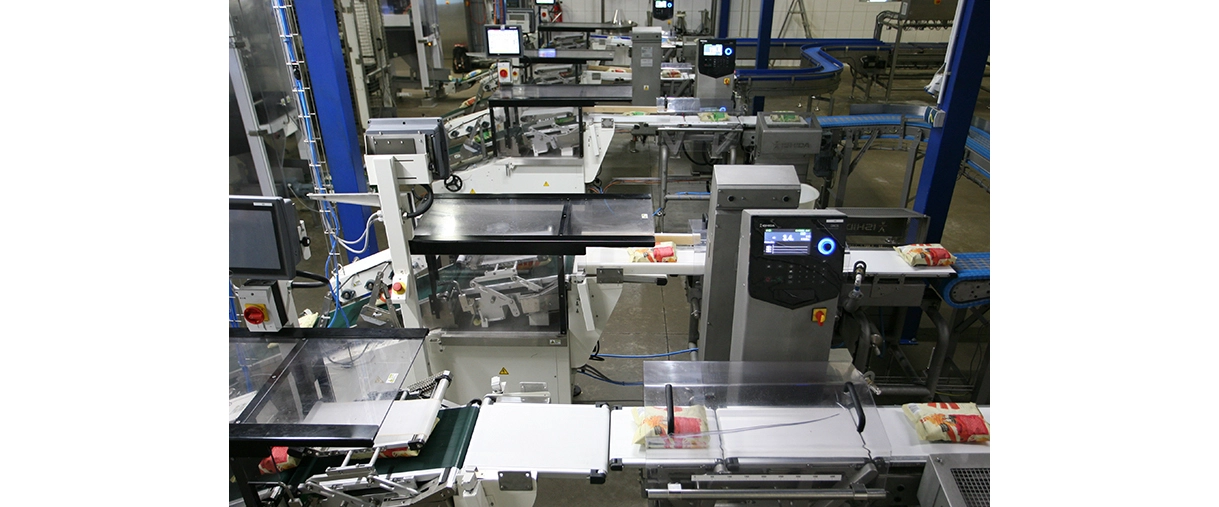
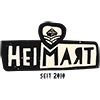
A specialist German potato chip brand is maintaining excellent quality control on its recently upgraded high-capacity packing lines thanks to the introduction of Sealtesters and Checkweighers from Ishida Europe. Krosse Kerle potato chips from Johanning Snack are cooked with their skins intact and produced from potatoes picked from fields right next to the factory.
Facts and Figures
Efficient
The Ishida DACS-G checkweighers minimise product giveaway due to overfilling.
Flexible
The Ishida sealtesters and checkweighers deliver a seamless, totally reliable quality control solution capable of operating at high speeds, for example up to 85 packs per minute for a 115g bag, with only the upstream systems preventing them from achieving even higher speeds.
Accurate
The Ishida TSC-RS sealtesters are fully automatic inline systems that can detect leaks with diameters of just 3mm at speeds up to 150bpm.
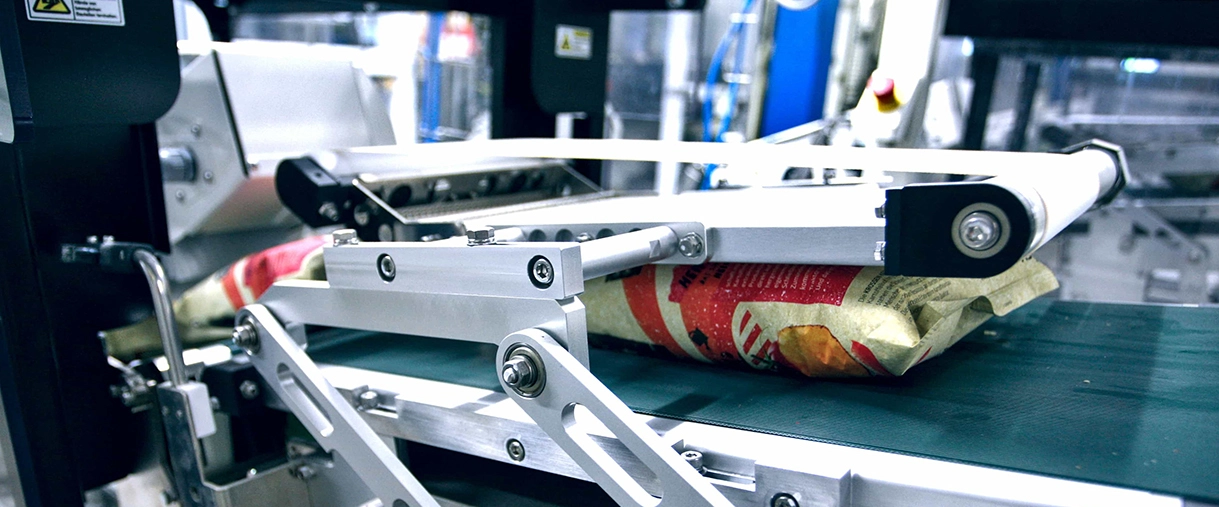
Challenge
Available in four flavours, the crisps are made of slices cut from whole potatoes and are twice as thick as most of the varieties found on supermarket shelves. A special process is used to fry the crisps slowly and gently at low temperatures to give them their characteristic extra crunch, as well as a reduced fat content.
The company produces 12 different pack formats with fill weights ranging from 20g to 200g. When the end-of-line packing systems were automated in 2018, it meant upgrading to state-of-the-art quality control facilities as well. Employees had previously checked the density of the sealed packets by hand, and weight monitoring was a matter of spot checks.
Solution
The Ishida sealtesters and checkweighers deliver a seamless, totally reliable quality control solution capable of operating at high speeds, for example up to 85 packs per minute for a 115g bag, with only the upstream systems preventing them from achieving even higher speeds. 'Ishida was the only supplier to offer both sealtesters and checkweighers in one package,' explains André Wurz, technical manager at Johanning Snack. 'Not only that, but our previous experience with Ishida for other packaging machines in our production facility had been excellent'.
The Ishida TSC-RS sealtesters are fully automatic inline systems that can detect leaks with diameters of just 3mm at speeds up to 150bpm. Because the packs are full of fragile crisps, the extremely careful way in which the sealtesters handle them is a particularly useful feature.
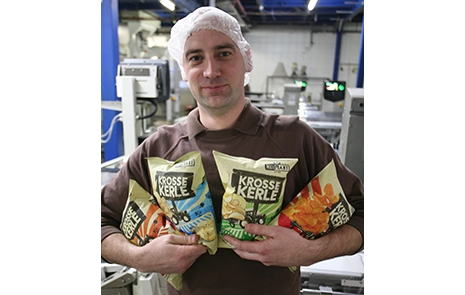
IDCS II tells us what we need to know about line output, with IDCS II, we can log every packet of crisps and then pass these logs on to our customers.
Crisps wedged at angles inside the packets can often create bulges, especially in smaller bags. Special brushes smooth out these lumps and bumps before the packets are inspected. This means that the packs are delivered to the sealtester’s inspection head in the most effective way possible, enabling it to test the seal integrity of every pack in line automatically. A servo driven pressure head allows the system to exert the ideal pressure without damaging the packaging or its contents.
The TSC-RS sealtesters are able to detect a wide range of defects. For example, packing material or product residue burnt onto the sealing jaws of the bagmakers can sometimes result in pinholes in the heat seal. Bits of product can often also find their way into the bottom seals of the crisp bags during filling, preventing the packs from sealing correctly. The system will also identify packs with holes in the seal areas. In addition, packaging that has not been sealed correctly and has open seals, or those that are sealed but the pack thickness is outside the set limits will be rejected by the sealtester during inspection and the machine can identify faulty bags caused by problems in the upstream bagmakers.
The Ishida DACS-G checkweighers meanwhile ensure that all finished packs comply with relevant regulations, rejecting any that fail to meet specifications. At the same time, the checkweighers minimise product giveaway due to overfilling. The machines’ high-speed loadcell delivers accuracy to within 0.2 grams, while a special system compensates for floor vibrations.
Operators can switch between two settings at the touch of a button, which means that the checkweighers can be used for a larger product range. Together with their quick changeovers, this makes the Ishida DACS-G models ideal for Johanning Snack’s requirements. The robust design also features a ‘dislocating force limiter’ function, which disconnects the highly sensitive weighing sensor from the belt before it can suffer any permanent damage from external impacts. It then immediately resumes operation. Equally important, the checkweighers incorporate Ishida’s IDCS II (Ishida Data Capture System) web-based software that collects a wealth of data about every single pack to provide valuable information that helps Johanning Snack boost productivity. IDCS can carry out real-time analyses based on product batches, shifts, operators, products, machines or lines, with graphical displays and reports that are user-defined and can be customised. The parameters can be accessed online during production and direct process adjustments can be made. The Ishida software is compatible with systems such as SAP or SCADA, and data transfers can be carried out to programs such as Microsoft Word, Excel and Adobe PDF.
Ishida Europe Seal Tester
Ishida's Atlas packaging system with seal tester integration.
Such a combination of checkweighers and data analysis is a control function that Johanning Snack considers very useful from a business management point of view. If the figures produced do not match the targets, the operator can immediately make the appropriate adjustments. 'IDCS II tells us what we need to know about line output,' confirms André Wurz, adding that the software is also 'very interesting' for his colleagues in quality assurance. 'With IDCS II, we can log every packet of crisps and then pass these logs on to our customers,' says Wurz, who is able to use the system on a mobile device even when away from the factory.
Johanning Snack is reaping the benefits of investing in fully automatic quality control. The Ishida systems work faultlessly in three-shift mode. Operators can carry out product changeovers, which usually take place twice daily, very quickly by calling up pre-sets. 'We have maintained full and exceptionally reliable quality assurance while saving on expensive manual labour at the same time,' says Wurz, summing up the benefits of the new machines.
Download case study

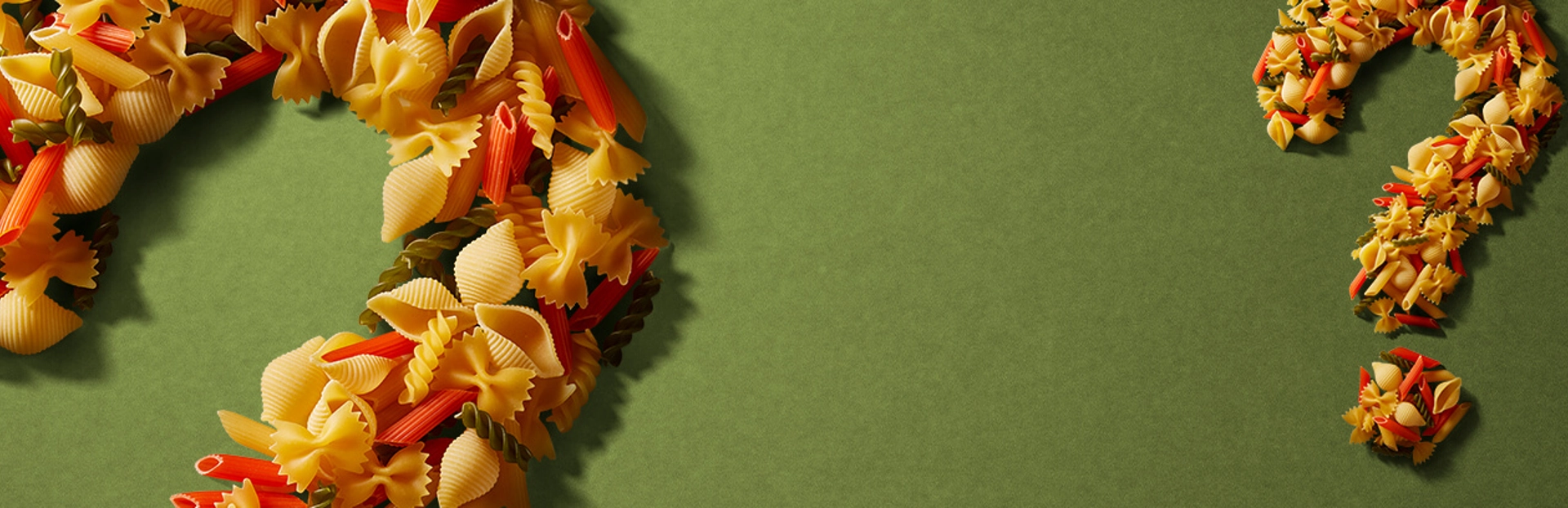
Speak to an Ishida expert
Every business has its own challenges; ours is to help you overcome yours. Working smarter, faster, together, we can help you achieve higher standards and get your products retail ready quicker.