Innovative Leak Detection Technology Benefits MAP Quality Control
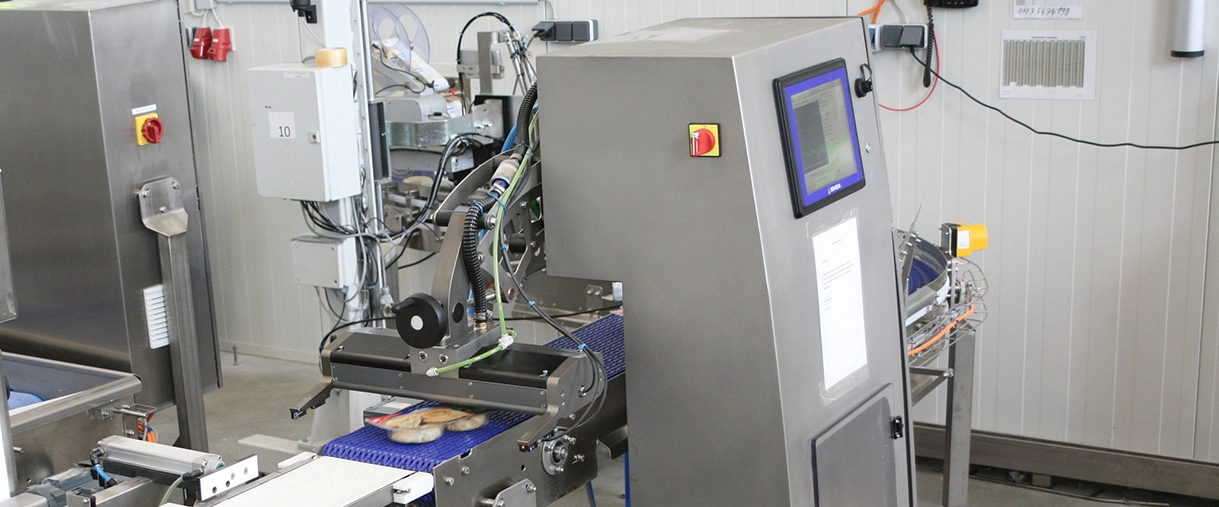
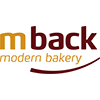
Ishida’s revolutionary AirScan inline system for detecting leaks in MAP packs has greatly enhanced the quality control procedures, as well as reducing labour costs, for a new snack product from M-Back GmbH in Germany which is being produced for dairy giant Meggle.
The “Ofen Schnecke” is a small puff pastry product that is available in two versions, filled with a combination of feta cheese and fresh herbs or spinach. The rolls, which need to be warmed up in the oven before consumption, are packed in thermoformed trays each containing two or three products, with fill weights of 180g and 300g.
'We used to perform a visual inspection of smaller batches,' says Marcel Schwebler, head of the packaging department at M-Back. 'However, this process was no longer practical, as output had increased significantly. So we looked for a fully automatic quality control solution that is 100% reliable'.
Facts and Figures
Efficient
The Airscan can reliably find holes with a diameter as small as 0.25 mm, at breath-taking speeds of up to 180 packs per minute.
Accurate
In two-shift mode, the Ishida AirScan checks 3,500 packs of “Ofen Schnecke” per hour, which equates to a belt speed of 30 metres per minute.
Flexible
The high-performance system checks each individual tray in less than 20 milliseconds for traces of escaping CO2.
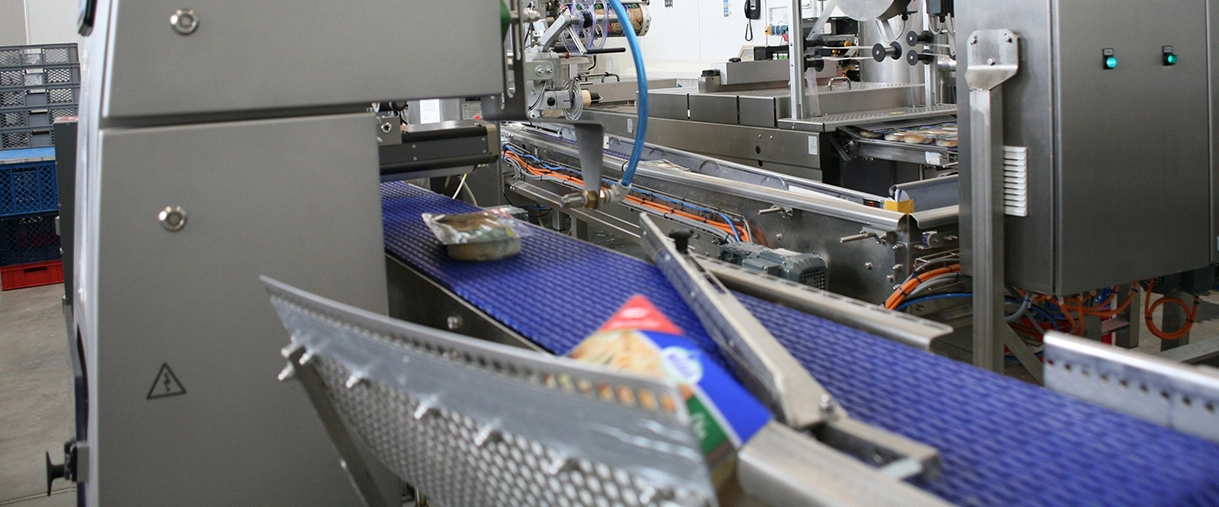
Challenge
When the delicate puff pastries are packed, it is not uncommon for product traces to get into the sealing area of the trays. This can result in leaks, which may cause protective gas to escape and draw in moisture. In rare cases, external factors can also cause holes in the film. If such defective packaging is not withheld from distribution, the shelf life can be significantly reduced and the product appearance can suffer. M-Back’s specification was to reliably identify leaks with a diameter of 0.4 mm or above.
Solution
Ishida AirScan uses laser technology to detect leaks of carbon dioxide (CO2), which is used in many MAP applications. The high-performance system checks each individual tray in less than 20 milliseconds for traces of escaping CO2.
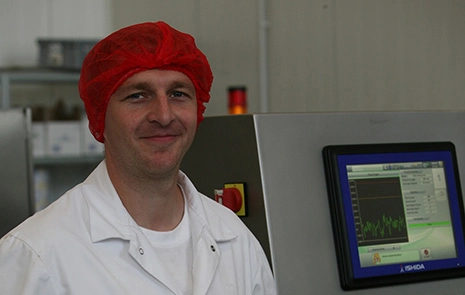
The Ishida AirScan inline leak detection system is worth its weight in gold to us!
The Ishida Airscan can reliably find holes with a diameter as small as 0.25 mm, at breath-taking speeds of up to 180 packs per minute. Users will improve their product quality without any adverse impact on products, as the inspection process does not exert any pressure - unlike conventional inline seal testers - and is therefore completely non-destructive. The inline system can be integrated into existing packing lines in a few minutes, without requiring any modifications to existing conveyors.
The Ishida AirScan at M-Back has been placed at the end of the packing line, between other control systems and a labeller. Since its installation, quality assurance has reached new levels. About 3% of packs are identified as having a leak. These are eliminated using an air reject mechanism and transported to a collection chamber for subsequent repacking. 'We definitely find even smaller holes than 0.4 mm,' Marcel Schwebler reports. 'By way of illustration, if you immerse the packs that have been found to be faulty in a water bath, you won’t see any gas coming out. In a laboratory, however, we can detect changes in the composition of the gas mixture'.
There’s no alternative to the AirScan system when it comes to speed.
Ishida AirScan
This revolutionary leak detection system makes a real and immediate difference to the seal integrity of your tray packs.
In two-shift mode, the Ishida AirScan checks 3,500 packs of “Ofen Schnecke” per hour, which equates to a belt speed of 30 metres per minute. 'There’s no alternative to the AirScan system when it comes to speed,' says Marcel Schwebler. He also highlights the system’s userfriendliness and availability, pointing out that it is very easy and safe to operate and requires only minimum maintenance.
No changes to settings are needed for product changeovers; only the height-adjustable control arm with the sensor head needs to be adjusted to the different pack heights. Dry cleaning before and after each production batch is completed within ten minutes.
Download case study

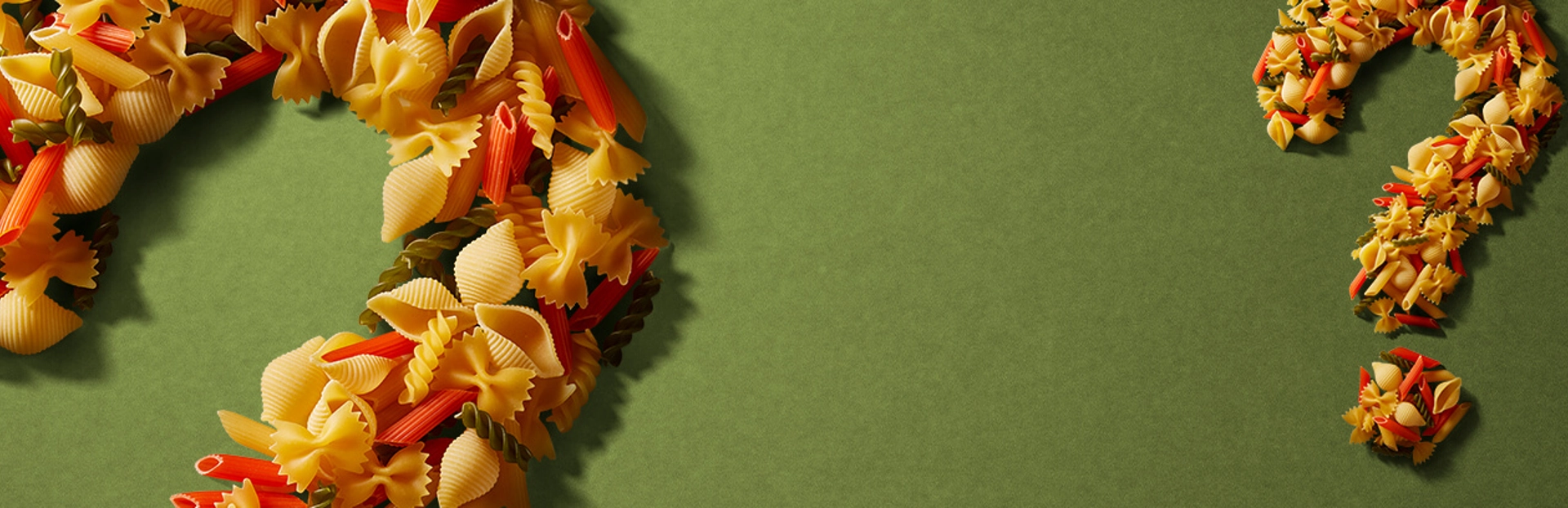
Speak to an Ishida expert
Every business has its own challenges; ours is to help you overcome yours. Working smarter, faster, together, we can help you achieve higher standards and get your products retail ready quicker.